Digital Exclusive: The future of gas turbines in the green revolution
Author. S. HINER, Parker Filtration Group, Alton, Hampshire, UK
With the rise of renewables wreaking dramatic changes to gas turbine operational modes, there is now an increased focus on minimizing operational costs. Gas turbines may be here to stay, but filter systems must remain relevant and efficient, as well.
While today’s gas turbines run almost exclusively on fossil fuels like natural gas, it would be a misconception to consider them obsolete technology. Not only are gas turbines extremely efficient, but they possess qualities that are not just desirable but will remain essential even in a future energy system completely separated from the carbon-emitting fuels that presently dominate it.
One of the most important characteristics of gas turbines is their ability to quickly ramp output up and down in response to fluctuating demand. In a world increasingly dominated by variable output renewables like wind and solar, this ramping capability will persist as vital in maintaining constant energy supplies to avoid blackouts and brownouts. As a grid-connected generator with a large rotating mass, gas turbines also play a crucial role in stabilizing the electricity grid and ensuring that important parameters like voltage and frequency remain constant.
Additionally, the installation of new gas turbine power plants is much quicker than for most other forms of power generation. This is another flexibility play in which gas turbines can be installed rapidly and at scale to add power as necessary, support renewable energy operations or bolster distributed generation, and deploy in areas where the existing electricity transmission and distribution grid is weak or does not exist and cannot support new power supply and demand requirements.
Indeed, even if gas turbines continued to run on fossil fuels, it is almost certain that the energy system would still require them—however, this is changing, too. With appropriate modifications, gas turbines can burn almost any fuel, and large original equipment manufacturers (OEMs) are already developing gas turbines that can run on a blend of hydrogen (H2) or even 100% H2 or other green fuels.
Therefore, gas turbines can already run on a carbon-free fuel that can be generated from renewable electricity and the electrolysis of water. Gas turbines can also use ammonia and biofuels that also remove the carbon from the power generation equation. While we cannot necessarily predict the precise mix of future green fuels, we can safely bet that future gas turbines will be burning whatever fuel ends up winning the race to become an alternative to natural gas.
It is clear then that while gas turbines are often perceived as a temporary bridging technology until renewables can be deployed at an even greater scale, this could not be further from the truth. While the core turbine technology will not significantly change, the operating regime for gas turbines is already changing—this trend is likely to continue for some time.
Changing operations for gas turbines. One of the most profound changes affecting gas turbine operation has been the diminishing requirement for base load capacity. In previous decades, gas turbines would have typically operated at full power for ~8,000 hr or more per year and were only shut down for periodic servicing. The rapid changes of the last decade have left this desirable scenario far in the distant past.
Renewables now get priority despatch, leaving gas turbines to pick up the slack only when there is insufficient wind and solar to meet demand. As so-called peaking units, most of these machines switch on and off multiple times per day and typically ramp up and down during periods of operation. This switch for gas turbines typically sees machines operate for hundreds of hours a year rather than thousands and has thrown the conventional economic and business cases for gas turbines into disarray. So, while gas turbines are certainly here to stay and will form a significant part of the energy mix even once the clean energy transition has been completed, new operating models place far greater emphasis on operational costs (OPEX) than ever before as owners look to balance the books on far fewer operating hours.
The continued importance of filtration. This increased scrutiny of operations and maintenance costs extends to ancillary systems, such as the components that make up the air inlet filtration unit. This system remains critical to the efficient operation of the gas turbine and, if anything, will become even more important given its role in maintaining the gas turbine at peak performance. An effective filtration system also achieves this while minimizing costly maintenance operations (e.g., compressor wash cycles).
However, with the filter elements now operating for far fewer hours per year, their lifespan may no longer be determined by unacceptable pressure losses due to becoming clogged with dust, particulates or pollution. Indeed, rather than being viewed as a regular wear item that might be replaced annually or even more frequently—particularly in dusty or harsh environments—filter elements may instead last many years before plugging significantly increases their pressure drop. Under these conditions, filter longevity may be determined by other factors and could potentially become a significant OPEX in today’s operating regimes.
Where life extension counts. Given the role of the gas turbine and how its operational parameters are evolving, so too will the filtration system to ensure optimal performance under any circumstances. These changes have driven multiple modifications to filtration systems that improve and maximize filter longevity to reflect these new operating modes. Filter cartridge frames are exposed to corrosive contaminants (e.g., salt water) that can accelerate rust and reduce the frame’s lifespan. While this may be an insignificant issue in filter cartridges that are replaced annually, with lifespans now running into years, this corrosion can come to represent a substantial operational cost.
To eliminate this overhead, the author’s company, for example, has improved the construction materials of its filters to maximize their lifespan. The company’s range of cartridge filtersa already features G90 galvanized steel, whereas standard galvanization for cartridges is the lower specification of G60. In addition to improved galvanization, the frames are also powder coated and designed to last far longer than standard filters and provide greatly improved corrosion protection (FIG. 1).
FIG. 1. Samples of filter mesh with G90 coating (left) vs. a powder-coated G90 cartridge filtera (right) after 840-hr ASTM B117 salt spray challenge and tensile test.
All other materials that go into the cartridge filtera range are top-quality polyurethanes that are sourced from first-tier manufacturers to guarantee long-term adhesion and sealing performance. Other factors that improve filter longevity go beyond material choices. Filter cartridges are deployed in challenging environments and are subjected to vibration, pressure changes, temperature and humidity changes, and other environmental factors that can impact lifetime performance. Top-quality “fit and forget” stability has become much more important when filter cartridges are expected to remain in service for years without allowing materials breakdown, poor dimensional stability or other factors to allow filter bypass.
Additionally, these considerations extend beyond the primary filtration system—each system usually contains other filters and additional components such as evaporative coolers that are deployed in many gas turbines. Materials choices such as 316 stainless-steel frames, plastic framing for pre-filters and robust cooling media are all built into a system that supports the new reality of gas turbine operations.
Gas turbines are certainly here to stay; however, given the current state of flux and market uncertainties facing the gas turbine business model, even potentially small improvements in OPEX can add up to a compelling business case.
NOTES
a Parker Hannifin’s “Assure” range of cartridge filters
ABOUT THE AUTHOR
STEVE HINER is the Chief Engineer for the Parker Hannifin – Filtration and Energy Solutions Division. He is internationally recognized in the industry as one of the world’s leading experts for gas turbine inlet air filtration with more than 30 yr of GT specific air filtration, development, testing and application experience across all markets—marine, offshore and land-based—with technical relationships with most GT OEMs and many end users.
Hiner has many granted patents to his name, has published many papers and articles, and participated extensively in panel sessions at conferences. He has contributed significantly to many GT OEM and end user specs and is a committee member expert for ISO 29461 and a contributor to the API616 standard. Hiner is also a paper reviewer for ASME and a member of the core filtration group for ETN Global association. The author can be reached at steve.hiner@parker.com.
Related News
Related News
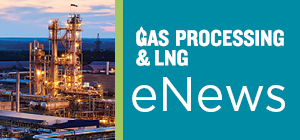
- Egypt agrees to buy up to 160 LNG cargoes through 2026
- TotalEnergies CEO expects to restart Mozambique LNG project this summer
- TotalEnergies and CMA CGM to launch LNG bunkering logistics JV to accelerate maritime decarbonization
- Renergen awards EPCC contract for Tetra4 LNG and helium project
- thyssenkrupp nucera acquires modular high-pressure electrolysis solution from Green Hydrogen Systems
Comments