Water treatment specialist SurfCleaner supplies Norwegian energy giant Equinor
Swedish firm SurfCleaner has delivered a full ATEX SCO 1000 system to Eqinor’s Kårstø processing plant in Nord-Rogaland, the largest of its kind in Europe.
The plant plays a key role in the transport and processing of gas and condensate/light oil from major sites on the Norwegian continental shelf.
SurfCleaner is the world’s-first skimmer hybrid technology. It is capable of highly effective separation, removal and recovery of floating water contaminants. The core principle behind the technology was developed by clinical physiologist Dr. Stig Lundbäck following his discovery of the human heart’s dynamic adaptive piston pump (DAPP) functionality.
Equinor’s refineries, processing plants and terminals transform crude oil and natural gas into everyday commodities such as petrol, diesel, heating oil and consumer-ready natural gas. Around 30 fields are connected to Kårstø via pipelines, and millions of cubic meters of gas and condensate/light oil flow into the plant every day. There, the heavier components are separated out, while the rest, which is called dry gas or sales gas, is piped onwards to the continent. Around 90 MMm3d of rich gas can flow through the plant.
At the processing plant, wet gas [natural gas liquids (NGL)] is separated from the rich gas and split into products including propane, normal butane, isobutane, naphtha and ethane. Propane is stored in two large rock chambers (caverns) with a total capacity of 90,000 metric t, while butane, isobutane, naphtha and ethane are stored in tanks. Production of liquefied petroleum gas (LPG), ethane and stabilized condensate/light oil results in around 500 tanker dockings per year, meaning that the Kårstø plant ranks as the world's third largest producer of LPG. Meanwhile, dry gas is exported from Kårstø via the Europipe II pipeline to Dornum in North Germany and through the Statpipe and Norpipe pipelines to Emden.
SurfCleaner Founder and Chief Sustainability Officer Christina Lundbäck said the deal marks another significant breakthrough for the firm. “We are thrilled to be expanding in the processing sector across Scandinavia,” she said. “Despite the fact that many processing industries are trying to decrease by-production of wastewater, a vast amount of cooling water and process water still needs to be treated. Some industrial plants use their own specialized facilities to treat wastewater, such as API separators and wastewater process tanks. Others need to transport it to an offsite wastewater treatment plant. SurfCleaner provides effective technology for both situations: Skimmer Separator Hybrids SCO 1000 and SCO 8000 are highly effective, cost-efficient additions to existing facilities, or they can be used directly onsite to skim, separate and recover all types of oil and floating pollutants from the water surface. The recycled oil is pure and ready to be reused. SurfCleaner’s control system can also be easily integrated with SCADA, providing our clients with process data and traceability.”
The principle behind the technology is Dr. Lundbäck’s discovery of the human heart’s DAPP functionality. He built on DAPP to invent and develop the SurfCleaner—but he also applied other universal laws of physics from nature and the universe, such as gravity, equilibrium, variation in rotation velocity in the center and the periphery, different density, and more.
This makes the SurfCleaner a truly unique machine, working in concert with the laws of nature rather than trying to combat them. The technology is enhancing gravity by setting the liquid in vertical and horizontal motion inside the body of the SurfCleaner—creating a circular inflow at the top, and an outlet at the bottom—the rest is just pure physics. The SurfCleaner needs no pump, no powerpack, no hydraulics and no pneumatics. This helps the SurfCleaner to be efficient and cost-effective.
Highlights and values achieved by the SurfCleaner technology include:
- Collection, separation and discharge of the contaminant is achieved within one efficient unit: This reduces complexity, energy consumed within the process (150 W at 8m3 oil separation) as well as making the operation process easy to handle.
- A large collection area enables stationary or semi-stationary installations (the unit does not need to move around to achieve a high collection capacity for a large area).
- Intelligent technology: The unit can be controlled and monitored remotely, minimizing exposure to personnel in hazardous environments.
- 24/7 operation and aggregation of data: Cost efficient, and the collected data can easily be uploaded (e.g., into a sustainability report).
- The technology allows for the effective collection and separation in varying conditions (e.g., with varying thickness levels of hydrocarbons, as well as floating debris).
- Verified technology with a clear legacy: Units have been in operation for more than 20 yr with minimal need for maintenance, due to only two moving parts.
SCO 1000 features include:
- Lightweight, less than 30 kg, easy to move and handle
- Requires no pump, no powerpack, no hydraulics, no pneumatics
- Low power operation, 20 W on average
- Remote control via smartphone/tablet
- Data output over how much oil is collected over time, and electricity consumption
- Automatic removal and separation of oil with up to 99.5% separation
- Separate up to 1,000 liters/hr of pure oil
- Continuous unmanned/remote operation with minimal service requirements
- No noisy generators needed, allowing recovery in sensitive areas
- ATEX/EX certified for Zone 0
SCO 8000 features include:
- Automatic removal and separation of oil with up to 99.5% separation capability
- Capacity to collect and separate up to 8,000 liters/hr of pure oil
- Continuous 24/7 operation with minimal service requirements, even over long periods of time
- Low power operation, 150 W on average
- Energy and cost-efficient operation with low maintenance, enabling substantial cost savings
- Easy handling, installation and service
- ATEX/EX certified for Zone 0
- SCADA integration
- Data output over how much oil is collected over time, and electricity consumption.
Related News
Related News
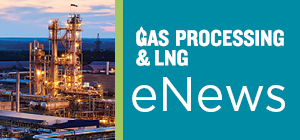
- U.S. ethane exports to China hit new roadblock with license requirement
- Australia clears Woodside to run North West Shelf LNG plant to 2070
- Egypt agrees to buy up to 160 LNG cargoes through 2026
- Shell to add up to 12 MMt of additional LNG capacity by 2030
- Woodfibre LNG sets new benchmark as world’s first net-zero LNG export facility
Comments