ConocoPhillips boosts processing efficiency with new Zia Hills Central Facility
KEY POINTS:
- This is ConocoPhillips’ fifth central processing facility in the Permian Basin
- New Mexico facility uses electric compressors to reduce emissions
- Centralized design delivers economic gains, lowers operating expenses
- Safety success for project: 177,000 work hours with zero recordable injuries
- Project delivered on time and under budget despite inflationary pressures
ConocoPhillips’ newest central processing facility is significantly enhancing the company’s Zia Hills asset in New Mexico by optimizing operational costs, expanding processing capacity, reducing surface footprint and curbing emissions.
Known as Zia Hills Central Facility 2 (CF2), this Delaware Basin East facility is integrated with its 2020 predecessor, Zia Hills Central Facility 1 (CF1). This looped infrastructure supports the development of Zia Hills, a 13,000-acre federal exploratory unit covering an oil-and-gas field known for its stacked layers of hydrocarbon-bearing rock.
CF2, which came online in January 2024, can process up to 30,000 barrels of oil per day and 75,000 barrels of water per day compared to CF1, which can process up to 18,000 barrels of oil per day and 30,000 barrels of water per day. Both facilities can process 120 million standard cubic feet of natural gas per day.
“CF2 was an impressive execution success for the company due to excellent project management,” said Delaware Basin East Asset Manager Hal Mead. “The key to the project’s success was involvement of the Operations team in every step along the way, from design to execution. The project was impressively on-time and under budget during an inflationary time-period, achieving all business objectives while having zero recordable injuries.”
Best-in-class transportation and processing costs. Oil, gas and water are initially separated at the wellhead before being sent to CF2 for processing. ConocoPhillips sells the processed oil and gas to third-party customers, while a third-party vendor takes the produced water for recycling or disposal.
CF2 offers significant advantages to third-party oil and gas buyers. Instead of building pipelines to individual well pads, CF2 allows multiple pads to feed into one location. This centralized setup provides a steady flow of oil and gas over a long period, increasing commercial flexibility and incentivizing third-party buyers to bid for the company’s high-specification hydrocarbons. Consequently, ConocoPhillips has been able to negotiate better rates for its oil and gas.
CF2 is also delivering economic gains in terms of water off-take and artificial lift. At CF2, the cost of water off-take is notably lower than at individual pads. Additionally, the facility recycles gas back to the well pads for gas lift. Unlike decentralized setups that have a dedicated compressor for each pad or well, CF2 has a bank of electric compressors servicing the lifting needs of the Zia Hills wells. This centralized setup makes operations more efficient and reduces operating expenses.
Enablers for a central hub. The success of CF2’s centralized design relied on two key factors: abundant contiguous acreage and the company’s ability to provide upfront capital. The Zia Hills asset, with its consolidated core acreage, facilitated the effectiveness of this centralized approach, supported by the company’s financial capacity and expertise. CF2's centralized approach also decreases the overall surface footprint by more than 200 acres due to smaller well facility pads and less equipment needed across the field.
“The enhanced economics of the individual wells more than makes up for the initial investment,” said Reservoir Engineer Mark Woodward, whose expertise ensured that the economic viability of the facility was sound.
ConocoPhillips has identified approximately 300 to 400 future wells that can be drilled and integrated into CF2. This drill-to-fill approach is facilitated by the multi-layered formations found at Zia Hills.
“Zia Hills will benefit by producing into the centralized system," Woodward said, "and we can continue to feed CF2 by sending new production streams to this facility for the next 15 years.”
Reservoir Engineering Supervisor Brian Thompson said CF2 is integral to the development of Zia Hills, a best-in-class asset.
“On top of the economic and environmental benefits,” he said, “the holistic approach we are taking in Zia Hills allows us to optimize development plans. Having offtake capacity at CF2 allows us to appropriately plan our rig schedule, infill degradation plans and spacing and stacking strategy.”
'One of the best facilities we've ever built'. Staff Facilities Engineer Juan Casanas, who played a pivotal role in overseeing the design, construction and installation of CF2 as well as the company’s four other central processing facilities in the Permian, enthusiastically described CF2 as “one of the best facilities we’ve ever built.”
“One of the big successes for this project is the emission reductions compared to our other central facilities in the Permian,” Casanas said, noting the CF2 design aligns with New Mexico’s environmental regulations. To reduce emissions, the facility employs electric compressors instead of gas-powered ones. CF2 also uses four Vapor Recovery Units (VRUs) and two heater treaters instead of three stabilizer trains to reduce additional emissions. The project has received all necessary permits and authorizations from state and federal agencies.
Casanas and the project management team drew upon insights gained from their work on prior central facilities to develop CF2. And by collaborating with Operations, they successfully optimized the facility’s functionality and design.
In the critical role of Operations liaison, Stabilizer Specialist Elijah Lindsey worked closely with the project management team to create a user-friendly design for CF2 operators.
Lindsey collected feedback from operators at CF1 and other Delaware Basin facilities. As a result, the project team made notable enhancements to the final design and functionality of CF2. In addition to incorporating electric compressors, Lindsey said the project team made several other crucial modifications. These included replacing stabilization towers with conventional heater treaters and optimizing the facility’s tank areas and gas recovery systems.
Operations Manager Carlos Blanco said such collaboration enabled the successful delivery of the facility in 2024, marking a significant milestone for the Lower 48 business unit.
“The assurance feedback loop was constant,” he said. “Operations' input proved invaluable to the final design. Our focus now lies on maximizing the throughput capacity of the facility, as this supports the economics of our centralized plan.”
Related News
Related News
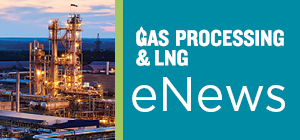
- Egypt agrees to buy up to 160 LNG cargoes through 2026
- Shell to add up to 12 MMt of additional LNG capacity by 2030
- ADNOC takes FID, awards $5 B in contracts for Phase 1 of its Rich Gas Development project
- U.S. ethane vessels stall amid curbs on exports to China
- TotalEnergies CEO expects to restart Mozambique LNG project this summer
Comments