Sponsored Content: Boosting the performance of natural gas sweetening membrane plants
INTRODUCTION
Although natural gas is considered a relative clean energy source, it comes from the ground in a mixture that often contains high concentration of CO2, which has some negative properties: it does not burn, and it reacts with water to form carbonic acid. Pipelines, gas turbines, heating systems, power plants, and engines would probably fail quite fast if they were operated with crude natural gas. Therefore, the availability of simple process technology to remove CO2 that can be applied in remote, unattended or offshore locations is highly desirable. Ease of operation, quick start-up, and high process availability are very important factors in addition to competitive capital and operating costs for the technology.
The dominant technology for CO2 removal is chemical absorption by Amines, which is widely used in the industry. Nevertheless, the natural gas sweetening market has a strong desire to look for process alternatives, since the amine technology has some drawbacks including ongoing chemical replacement, reliability of mechanical equipment, higher operating costs and environmental impacts (e.g. hydrocarbon emissions). Membrane systems overcome part of these drawbacks. They combine the advantages of lower operating costs, simple steady-state operational reliability, simplified turndown and expansion capabilities. Consequently, membranes were introduced to the market for natural gas sweetening applications in the mid 1980s. However, up to now membrane systems which are mainly based on cellulose acetate still have a minor market share. The factors used to limit the application of membranes include hydrocarbon losses, reliability of the membrane modules, lack of operational experience, a smaller reference list of membrane vendors and more stringent pretreatment requirements.
Despite the tremendous amount of research on new polymers for membranes, the major problem remains: the missing ability to demonstrate separation performance in field conditions through the proper scale-up of the membrane. For this reason, the same types of polymers, in particular cellulose-acetate, have been used for twenty years.
The drawbacks to these current polymers include low CO2/CH4 selectivity and therewith low methane yield and high sensitivity to heavy hydrocarbons and CO2 plasticization, which limit the reliability of membrane plants and increase life cycle costs.
A more sustainable, stable and high-selective separation depends basically on two factors: the ability to control intrinsic properties of a high-performance polymer and the ability to control the membrane-formation process of such a polymer. Considering the polymers in technical use, P84 polyimide combines the required features of high CO2/CH4 selectivity and a low tendency to plasticize over time. Based on this material-platform, Evonik developed a crosslinked, highly selective and stable membrane under natural gas process-conditions and together with Linde brought this technology to market readiness. In several commercial scale applications very good results in terms of achievable hydrocarbon yields combined with optimized hydrocarbon and plasticization stability was demonstrated.
MEMBRANE DESIGN AND TESTING
The separation performance of membranes is in primarily determined by the intrinsic properties of the applied membrane material. Therefore, a high-performance polyimide was developed and optimized regarding the demands and conditions for natural gas sweetening applications. The membrane is formed as a hollow fiber to maximize the membrane surface area resulting in a high productivity per volume ratio. The integrally asymmetric hollow fiber membrane is produced directly from a polyimide polymerization solution by a phase inversion-based production process in which a dense film is formed at the outer surface of the fiber supported by an open porous support structure.
The feed gas enters the pressure housing and flows inside the cartridge through holes in a protective sleeve and is consequently forced to flow through the structurally packed hollow fiber bundle. Fast permeating gas components like CO2 and H2O can enter the fiber lumen much easier than slow components like CH4 and other hydrocarbons; the permeate gas is finally collected in the center tube. The slow components pass the bundle and leave the cartridge at the retentate end. An adjustable seal ring guarantees securely separated feed and retentate gas zones. The retentate gas of the leading cartridge of a serial cartridge arrangement serves as feed gas of the next cartridge. Typically, three to five cartridges are connected in series in the same housing.
This offers the advantage of minimizing the costs for valves and flanges. The design for these hollow fiber cartridges matches the flow configuration of standard 8” spiral wound cartridges and work as a plug-in replacement without any requirement for further adaptations to the existing equipment, thus reducing the costs when replacing standard 8” spiral wound cartridges since the expensive pressure housing does not need to be replaced.
In order to evaluate the potential of membranes in commercial applications, it is necessary to understand both their fundamental behavior (e.g. by binary gas experiments) as well as the final properties under operation conditions and gas compositions. Extensive test capabilities were established to evaluate the membrane performance from lab to production scale. A laboratory test set up is used to characterize the fiber performance and mimic real processing conditions to identify the influence of mixed gas effects under high pressure and temperature. Therefore, the set-up allows to vary feed gas conditions and to precisely dose higher hydrocarbon concentrations by an evaporator.
The effect of higher hydrocarbons on the CO2/CH4 selectivity for various operating conditions and feed gas composition is shown. It could be demonstrated that the selectivity is not affected by the presence of higher hydrocarbons, which confirms the strong chemical robustness and low tendency for plasticization. This stable performance is achieved by the high degree of crosslinking of the polymer chains effectively resulting in an infinite polymer-chain.
At the same time, the membrane features a very high stability in the presence of high CO2 partial pressures. The CO2/CH4 selectivity is even increasing with the CO2 partial pressure validating that there is no CO2 plasticization observed up to a CO2 partial pressure of 50 bar, which was the maximum tested CO2 partial pressure.
First tests were conducted to evaluate the membrane performance in the presence of H2S, which is known to degrade state of the art membrane materials. There is no change in selectivity with a H2S content of up to 1 vol.% indicating the high chemical stability to H2S. The CO2 permeate flow however is slightly reduced due to competitive sorption effects between CO2 and H2S, which is also transported through the membrane to the low pressure permeate side and therewith removed from the CH4 rich product stream.
Furthermore, different laboratory and pilot test setups are built and operated by Linde to identify and study the membrane performance for different module sizes and configurations.
A laboratory test setup with a gas recycle for long-term testing and high-end analytics has been prepared. With this plant, various gas mixtures can be prepared for the investigation of the membrane’s general performance data. To validate these general membrane performance data in commercial sized cartridges, different pilot setups for large gas flows have been installed. With the setup, scale up factors from lab scale to commercial scale modules are investigated. In this plant, representative gas mixtures can be tested in a single throughput.
For the test of the membrane cartridges under realistic process conditions, including trace components, a mobile test unit is used. This setup, includes basic pre-treatment units for the membrane and can be installed in various applications, like synthesis gas or natural gas plants.
REVAMP OF PLANT AT CUSTOMER’S SITE
General description
This section describes the experience following the replacement of spiral wound cellulose acetate cartridges with hollow fiber high-performance polyimide membrane cartridges. The client has been operating a natural gas sweetening plant for several years at one of his gas fields. The processed gas is an associated gas with a significant heavy hydrocarbon (HHC) content and elevated concentration of CO2.
Plant setup
The setup of the natural gas sweetening plant is schematically shown. It consists of a two-stage membrane plant arrangement. Dry feed gas enters a Joule Thomson (JT) skid, where the hydrocarbon dew point of the gas is reduced, and a booster compressor compensates the resulting pressure drop. The stream is then mixed with the recycle stream of the second membrane stage and sent to the first stage pre-treatment. In the first membrane stage, the CO2 content is reduced to the desired level in the residue/sales gas. The permeate of the first membrane stage still contains considerable amounts of methane, so it is recompressed and sent to the second membrane stage to increase the CH4 recovery rate. CO2 is removed at high concentration in the off gas and sent to a flare.
Feed gas and operational challenges
A CO2 partial pressure of approx. 22 kg/cm2(g) and a C5+ content of up to 4000 ppmv are very challenging conditions for common cellulose-acetate membranes due to their high sensitivity to plasticization. This led to a decrease in selectivity and CO2 removal capacity of the membranes.
Additionally, strong fluctuations of the CO2 content in the feed gas made a continuous and steady operation of the membrane plant difficult.
Furthermore, a second recycle compressors needed to be operated simultaneously as the capacity of a single compressor became insufficient.
When the plasticized membranes were not replaced regularly, physical damage to the membrane sheets occurred, which caused an increased permeate flow and low selectivity of the first membrane stage. Following, the compressor load further increased, and the membrane plant became more and more inefficient. Additionally, the trip of one of the two compressors required the shutdown of the complete membrane plant, which was very unsatisfying regarding operational performance.
Demonstration of membrane selectivity
To demonstrate the superior performance of the new membrane, the cellulose-acetate cartridges of one bank of the first membrane stage were replaced with hollow fiber high-performance polyimide membrane cartridges (our) membrane cartridges. Their performance, especially the selectivity between CO2 and CH4 was analyzed and tracked for approximately one month.
The selectivity of the membranes reached a peak value after the first 10 days of operation and then stabilized at the initial value. The process selectivity between CO2 and CH4 was between 2.5 and 3 times higher compared to the membranes that were replaced.
During this period, the content of HHC in the raw gas to the membranes was fluctuating to values of up to 1 mol.% due to some unstable operation of the upstream pretreatment (JT skid). However, as proven by the measurements, the selectivity of the membrane was stable and did not show any significant dependency of the feed gas HHC content, which confirms the experimental results.
STABILITY AGAINST HHC
During this first test period, due to incorrect installation, a leak in one of the membrane module flange connections caused a local temperature-drop below the hydrocarbon dew point. Due to the very high content of HHC in the feed gas, condensation of these HHC occurred inside the pressure vessel. After removal of one of the cartridges, liquid gasoline dripped from the fiber bundle.
As no spare cartridges were immediately available at site and the affected cartridges did not show any physical damage, they were reinstalled into the pressure vessel. The membranes were then put back into operation and the relative performance of the contaminated cartridge and a cartridge that was not exposed to liquid HHC was measured for 48 hours. The relative performance of the contaminated membrane compared to the fresh membrane are plotted in Fehler! Verweisquelle konnte nicht gefunden werden.
After approximately 24 hours, the separation performance had recovered to the performance of the non-contaminated membranes. The membranes were not physically damaged by the local and limited formation of liquid hydrocarbons. Of course, condensation of hydrocarbons should be avoided, since the separation capacity of the membrane cartridge will drop considerably due to blockage of membrane area by liquids and thus the removal of the desired amount of CO2 would no longer be achievable. However, since upset conditions like the one described above can always happen during operation, a stable material can grant significant savings in customer’s maintenance budget.
FULL EXCHANGE OF MEMBRANES
After the successful demonstration of the membrane performance, all cellulose acetate-membranes of both stages were replaced with new membrane cartridges.
At first, the old cartridges of the second membrane stage were replaced as the impact on the overall process performance was larger than that of the first stage. After the successful startup and stable operation of the plant, also all cellulose-acetate membranes of the first stage were replaced. The performance of the plant was then tracked by measuring flows and compositions of the relevant streams.
The amount of sales gas increased by 3.7 %; the required compressor power was reduced by 9.5 % due to the reduced permeate flow of the first membrane stage. This helped to increase the product yield of the plant and thus the client’s revenue; at the same time the operational costs of the membrane plant were reduced.
Additionally, the CO2 concentration of the second membrane stage permeate was increased from 82.8 to 92.5 mol.%. This means a better CH4 recovery rate and a considerable decrease of the environmental impact by lost CH4.
Besides the decreased energy consumption, the reduced requirement of compressor capacity also allowed the client to shut down one of the two compressors and use it as spare for redundancy. This increased the overall availability of the plant and thus the revenue due to reduced downtime.
A further advantage of the new membranes is the mechanical robustness against pressure surges and back pressure. The cellulose-acetate membranes had to be partially replaced approximately every 6 months to maintain the required capacity of the plant due to their quick deterioration. To date, the new membranes continue operating and have shown a stable performance for over four years, helping to considerably reduce the number of planned and unplanned downtime of the membrane plant with increased overall productivity.
Furthermore, this figure shows that the difference of capacity at start of run conditions compared to the end of run is significantly smaller. This allows to design the plant with a reduced overcapacity for compensation of deterioration and which further contributes to save initial investment cost.
SUMMARY AND OUTLOOK
The superior performance of the Linde HISELECT® powered by Evonik membrane was verified and proven. The high selectivity reduced CH4 losses and the load of the recycle compressor. The better robustness and longevity enabled the reduction of regular maintenance cost and downtime. Therewith the revenue was increased by more than 3,7 %, not including the additional benefits from a significantly improved reliability, availability and therefore ease of operation.
For different other opportunities, the performance of the membranes was validated and proven, too. Tests with single membrane cartridges and complete membrane plant replacements showed stable selectivities between 20 and 30, depending on the CO2 concentration of the feed gas, temperature, pressure ratios and flow rate.
AUTHORS
Markus Priske
Head of Application Technology SEPURAN®
Evonik Fibres GmbH
Schörfling, AUSTRIA
Dr. Werner Escher
Director Natural Gas Membranes
Evonik Operations GmbH
Marl, GERMANY
Dr. Oliver Purrucker
Head of Business Development and Sales, Adsorption & Membrane Plants
Linde GmbH, Linde Engineering Pullach, GERMANY
Dr. Patrick Schiffmann
Group Lead Membrane Technology
Linde GmbH, Linde Engineering, R&D Adsorption & Membranes
Pullach, GERMANY
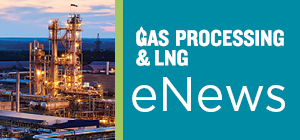
- ADNOC Gas awards $2.1 B in contracts to enhance LNG supply infrastructure
- Tecnimont to build waste-to-biogas plant to fuel local kitchens in India
- U.S. Department of the Treasury releases final rules for clean hydrogen production tax credit
- Indonesia regulator confirms disruption at bp's Tangguh LNG project
- Topsoe, Aramco sign JDA to advance low-carbon hydrogen solutions using eREACT™
Comments