Baker Hughes LM9000 confirmed as world’s most efficient simple cycle gas turbine after reaching key testing milestone for Arctic LNG 2
Baker Hughes announced the completion of the First Engine to Test (FETT) for the LM9000 aeroderivative gas turbine. The test took place at the company’s advanced turbomachinery testing facilities in Florence and Massa, Italy.
In December 2018, NOVATEK selected Baker Hughes for the supply of LM9000 aeroderivative gas turbines for the Arctic LNG 2 Project. The successful FETT completion paves the way for the supply of the same turbines for NOVATEK's new LNG projects.
The successful test completion confirms the LM9000 as the most powerful and most efficient aeroderivative gas turbine in its class with simple cycle efficiency in excess of 44% and a power output 15% higher compared to industry peers. This efficiency is key to driving lower carbon intensity, and combined with lower NOx emissions (15 ppm in dry condition, 40% lower than competing technology) makes for a more environmentally sensitive solution. A small footprint and innovative module design for fast and easy maintenance make the LM9000 the gas turbine of choice for all mechanical drive and power generation applications.
“This is a crucial milestone for the ongoing development of our innovative LM9000 turbine technology and an important step forward in the on time delivery of Arctic LNG 2, which continues to be on track despite COVID-19 challenges,” said Rod Christie, executive vice president, Turbomachinery & Process Solutions, Baker Hughes. “Building on our 30-year-plus track record of delivering highly efficient and reliable LNG technology, the FETT results are a strong recognition of the LM9000’s flexibility, reliability and suitability for major LNG projects around the world such as Arctic LNG 2.”
"The FETT results confirm the LM9000 turbine is the right choice for NOVATEK's LNG projects. In addition to better technical specifications, the machines also stand out in terms of environmental performance that will truly contribute to NOVATEK's strategy of producing the greenest LNG," said Igor Chasnyk, director for LNG projects, NOVATEK.
The successful FETT leveraged Baker Hughes’ turbomachinery remote testing capabilities to overcome travel restrictions imposed by COVID-19. More than 80 experts from various locations were connected remotely to perform the Full Speed and Full Load test. In addition, remote witness technology, such as smart glasses and helmets, enabled real-time and seamless sharing of machine inspections and virtual testing performed in Massa with the extended teams around the world.
Baker Hughes’ overall scope of work for Arctic LNG 2 includes the supply of turbomachinery equipment for power generation and three liquefaction trains on gravity-based structures (GBS) that will produce 6.6 million tons of LNG per year each, for a total production of 19.8 MMtpy
About the LM9000
The LM9000’s advantages include a 50% increase of meantime between maintenance intervals versus current aeroderivative technology – the longest in the industry. With the ability to start in a fully pressurized condition, and 24-hour engine swap capability, the LM9000 can also reach over 99% availability for best-in-class total cost of ownership.
Co-developed by Baker Hughes and GE, the LM9000 features a new driver specifically designed for the needs of LNG production. The design utilizes free-power turbine architecture that provides higher efficiency and enables the unit to operate over a wide range of speed settings from 2600 rpm to 3780 rpm with virtually unaffected power and efficiency. The free-power turbine also allows 50 Hz and 60 Hz power generation without needing a gearbox.
In addition to LNG applications both on and offshore, the LM9000 can provide simple cycle, cogeneration and combined cycle power generation to boost the supply of electricity to the world’s energy plants and power grids.
Baker Hughes has invested in producing uniquely designed engineering and manufacturing tools, test beds and equipment for the LM9000 in its Florence and Massa facilities in Italy.
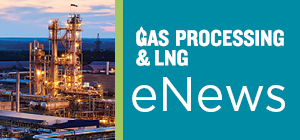
- ADNOC Gas awards $2.1 B in contracts to enhance LNG supply infrastructure
- U.S. Department of the Treasury releases final rules for clean hydrogen production tax credit
- Tecnimont to build waste-to-biogas plant to fuel local kitchens in India
- Indonesia regulator confirms disruption at bp's Tangguh LNG project
- Topsoe, Aramco sign JDA to advance low-carbon hydrogen solutions using eREACT™
Comments