GPA Europe '19: Optimizing pipeline design using AI
Adrienne Blume, Editor, Gas Processing & LNG and Executive Editor, Hydrocarbon Processing
AMSTERDAM—On Day 3 of GPA Europe's Spring Conference, Andrew Lewis of Augmented Engineering shared a presentation on the use of artificial intelligence (AI) to optimize pipeline network design.
Mr. Lewis started off by stating, "The hypothesis is that we needlessly spend too much money on pipelines because there are no optimization options in the early phases of design. If we could just save 1%, that would represent a considerable cost savings."
Pipeline cost factors. The main cost drivers for pipeline design are pipeline length, diameter and wall thickness. Changes in one parameter often require changes in the others. Pressure may also need to be increased, which can have further impacts on one or more of the other variables.
Route is another major factor in determining the cost of pipeline design, Lewis said. Although many possible routes exist, only one route results in the minimum cost. However, the best and least expensive route may not emerge from a manual comparison of different routes over different terrains and pressure requirements.
Algorithms for optimizing design. Pipetimize algorithms offered by Augmented Engineering utilize digitalized data (i.e., pipeline material cost, installation cost, geospatial data and pressure loss data) to calculate the most cost-efficient pipeline route.
If the pipeline is to be connected to a second well, the most optimum location for the tee must be determined. The Pipetimize algorithm automatically determines the least expensive configuration for a range of arrival pressures, Lewis explained. If three or more wells are considered, the number of possible configurations increases exponentially. Here, genetic algorithms can be used to calculate the best options of many.
However, manually tuning heuristics factors is time-consuming and complex. Machine learning and AI techniques can be applied to discover which heuristics factors are optimal. This minimizes the computation time required, while still discovering the optimum configuration for pipeline design with multiple wells.
Additional site design elements. OPEX and maintenance costs can be considered, and automated optimization can be performed to discover the maximum net present value (NPV). This approach to optimization for maximizing NPV can also be used to define optimum processing facility locations, optimum drill center locations and optimum reservoir profiles and phasing.
"We can find an optimum solution very quickly, and we can do this at the start of a project to determine where we should start looking [for the optimal route]. Going forward, this can be used for more detailed design," Lewis said.
The GPA Europe Spring Conference is taking place at the Shell Technology Center in Amsterdam, the Netherlands, from 15–17 May.
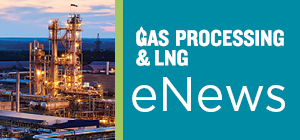
- ADNOC Gas awards $2.1 B in contracts to enhance LNG supply infrastructure
- U.S. Department of the Treasury releases final rules for clean hydrogen production tax credit
- Tecnimont to build waste-to-biogas plant to fuel local kitchens in India
- Indonesia regulator confirms disruption at bp's Tangguh LNG project
- Topsoe, Aramco sign JDA to advance low-carbon hydrogen solutions using eREACT™
Comments