Clariant Catalysts and Wuxi Xiyuan win further contracts for formaldehyde production projects in China
Munich, – Clariant, a focused and innovative specialty chemical company, announced that it will be collaborating with its engineering partner, Wuxi Xiyuan, in two new projects to supply their joint formaldehyde production technology. The new contracts, awarded by Shandong Yushiju Chemical and Shandong Sunny Wealth New Materials, will grow the number of customers using the partners’ advanced technology to six in a short period of time. The rapidly rising demand is due to the technology’s significantly higher efficiency and selectivity compared to the traditional silver-based method of formaldehyde production.
The innovative solution, based on Clariant’s high-performance FAMAX 200 DS catalyst, was recently installed by Wuxi Xiyuan in three formaldehyde plants in China and India. The fourth plant to use the technology will be located in the Jiangsu province of China. It is expected to commence operations in the second quarter of 2019 with a planned annual capacity of 240 kilotons of formaldehyde. The new customers, Shandong Yushiju Chemical, one of the largest Chinese producers of phenol formaldehyde resins, and Shandong Sunny Wealth New Materials, a leading antioxidant producer in China, will also start operating in 2019. The producers’ annual formaldehyde capacity is expected to be 150 and 130 kilotons, respectively.
Jiatao Zhang, Chief Operations Officer of Shandong Yushiju Chemical, commented, “To successfully meet the continuously growing demand for phenol formaldehyde resins in China, we aim to strengthen and streamline our operations to stay at the head of our field. We are convinced that we can achieve this with the progressive technology and catalysts provided by Clariant and Wuxi Xiyuan.”
Clariant’s FAMAX 200 DS is a next-generation formaldehyde catalyst which allows producers to achieve considerably higher productivity and profitability. The catalyst’s hollow, cylindrical shape reduces pressure drop over the catalyst bed by 10-15% compared to conventional catalysts. This special design gives producers the flexibility to reduce energy consumption when operating at the same plant capacity, or to increase production capacity at the same energy costs.
The iron-molybdenum catalyst also features an advanced chemical composition which improves low temperature activity and allows operation at reduced cooling medium temperatures. These characteristics, combined with higher reaction selectivity, further increase formaldehyde yields. Thanks to the catalyst’s ability to drastically reduce by-product formation, producers also benefit from higher formaldehyde quality.
Wuxi Xiyuan is a leader in formaldehyde production technologies for direct oxidation of methanol via fixed-bed catalytic reactors in China. The company’s latest strategy focuses on iron-molybdenum catalytic solutions for formaldehyde production due to the technology’s numerous benefits. Wuxi Xiyuan’s advanced process technology is a perfect match for Clariant’s world-class formaldehyde catalysts. After many years of collaboration, the companies entered a strategic partnership in 2017 to advance formaldehyde production in China.
Kevin Chan, Head of Business Unit Catalysts at Clariant in China, added, “We are honored to have been awarded two contracts by Shandong Yushiju Chemical and Shandong Sunny Wealth New Materials. Our strong partnership combines the capabilities of Clariant Catalysts and Wuxi Xiyuan to create additional value for our customers and to support the growth of the Chinese formaldehyde industry.”
With a long history in formaldehyde production, Clariant was the first to develop a ring-type catalyst to reduce pressure drop. Later, the company introduced a unique multi-layer bed system, which improves reactor performance by modulating the shape of the temperature profile. Clariant also created special automated machines for precise, rapid loading of multilayer catalyst beds, which reduce loss of production days during catalyst replacement. The company’s high-performance FAMAX catalysts and layer management solutions are tailored to customers’ plant conditions to optimize operations.
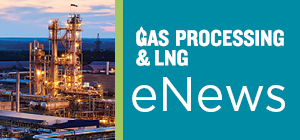
- ADNOC Gas awards $2.1 B in contracts to enhance LNG supply infrastructure
- U.S. Department of the Treasury releases final rules for clean hydrogen production tax credit
- Tecnimont to build waste-to-biogas plant to fuel local kitchens in India
- Indonesia regulator confirms disruption at bp's Tangguh LNG project
- Topsoe, Aramco sign JDA to advance low-carbon hydrogen solutions using eREACT™
Comments