GPA '17: Midstream Thought Leaders Forum pinpoints 10 issues for better gas processing/LNG performance
Adrienne Blume, Editor
SAN ANTONIO—Chuck Miller, Director of Global Gas Processing Sales and Marketing at Emerson Process Management in Houston, Texas, shared 10 key insights from the Emerson Midstream Thought Leaders Forum at a Tuesday afternoon presentation at the GPA Midstream Convention.
These 10 trends, Mr. Miller explained, are driving efficiency, reliability and the reduction of risk at gas processing and LNG operations.
Challenge 1: Equipment integration. The midstream must be able to integrate all devices, from the wellhead to the gas plant, to create a complete production and processing solution. Additionally, field personnel must have the ability to communicate with the pipeline operators and, in many cases, the plant operators.
"Operators would like to be able to communicate quickly and efficiently, and to be able to identify problems before they go to the field," Mr. Miller said. "So, integration of field data is key."
Challenge 2: Solution evolution. Gas processors have the ability to test new technology without the restraint of prior testing and qualification. "It's a different culture, and cultures are hard to change, but new technology comes out all the time," Mr. Miller acknowledged.
The Forum members acknowledged that midstream operators tend not to remove and replace equipment; rather, they operate and maintain it until the asset is obsolete or failing. "So, how do you solve those challenges, and what do they bring you from a return-on-investment standpoint?" Mr. Miller posited.
The Director also noted that the widest-ranging Forum conversation in this area centered on how to apply all of the reporting requirements developed over the past decades into control platforms.
"Being able to communicate to the field is key," he said. "How do we get critical information to the people in the field more quickly, in the event of a failure or other such anomaly?"
Challenge 3: Mobile client app development. Next-generation tools require application development, media connectivity, Industrial Internet of Things (IIoT) toolkits, database access, and changes in operations and maintenance culture.
"These will help to bring people with limited experience or skills up to speed very quickly, so that subject matter experts will be able to guide them and help troubleshoot quickly," the Director said.
Challenge 4: Cyber security. The Forum concluded that gas processing company IT departments, which are dictating most of the cyber security requirements, often lack a clear understanding of company operational systems.
Expertise and defense-in-depth strategies must be developed to comply with IEC 62443/ISA99 security standards, Mr. Miller said.
Challenge 5: Midstream process safety management practices. At present, gas plants implement safety instrumented functions (SIFs) with redundancy in the distributed control system (DCS) or programmable logic controller (PLC), versus safety integrity level (SIL)-related safety functions in an LNG facility.
Also, audits from the Department of Environmental Protection, the Environmental Protection Agency and the Public Utilities Commission are becoming more frequent and detailed, Mr. Miller noted.
"If [equipment] is SIL-rated, how can it go into the DCS?" he posited. "And if it goes into the DCS, how would you know to test it on a periodic basis?"
Challenge 6: Modular plants and standardization of design. The biggest advantage with modular plants is that the quality of fabrication can be controlled. Construction time can be managed, and inspections can be made on a more detailed and frequent basis.
"But how can we maintain project costs, schedule and quality of startup" when owner teams, interface equipment teams, automation contractor teams, EPC teams, and EPC back office locations are scattered throughout the world? Mr. Miller asked. "How can we do it right the first time? How can we provide project certainty?"
Challenge 7: Operability. Safety, remote operability and sustainability dictate how a system is engineered. If the equipment looks alike, it is beneficial. The value, Mr. Miller explained, lies in configurable systems, rather than programmable systems.
"We standardize on operator interfaces so that we can promote field personnel into operational roles," he noted.
Challenge 8: Reliability. Major downtime issues include equipment failure, slug water hitting a slug catcher, abnormal operating conditions, instrumentation and electrical work, or other operational anomalies.
Reliability issues typically evolve from scenarios where the plant cannot handle what is coming from the field, the Director explained. In this vein, two major problems are miscommunication between inexperienced field personnel and personnel not fully understanding their responsibilities.
Challenge 9: Recovery and throughput optimization. By 2018, Emerson expects more opportunities for optimization to emerge, especially when plant recovery modes change to higher levels of ethane.
"No one trusts closed-loop control, and most plants do not go back and optimize control loops," Mr. Miller said. "We agree that it should be done, but time is a big factor."
Challenge 10: Design for remote lifecycle support. In conclusion, Mr. Miller named a number of Forum-established benefits from remote lifecycle support, as well as design goals for midstream automation and lifecycle challenges for the midstream going forward.
Remote lifecycle support has a number of benefits:
- Organizes a response to a dynamic operation
- Drives collaboration between people and across disciplines, companies, and places via integrated multidisciplinary teams
- Distributes internal and external information and knowledge
- Reduces decision time and improves decision-making
- Distributes real-time utilization of scarce resources.
Midstream automation design goals include:
- Maximized product throughput
- Improved field and asset reliability
- Improved safety across the value chain
- Optimized recovery of high-value products
- Integrated management of field operations
- Maximized equipment availability
- Increased personnel efficiency under all operating conditions.
Finally, lifecycle challenges for midstream automation encompass:
- Seamless integrated control and safety systems (ICSS), PLC and supervisory control and data acquisition (SCADA) integration
- Integrated field-to-plant communications
- Multi-stakeholder, cultural commitments to improved efficiency.
The GPA Midstream Convention is taking place at the Marriott Rivercenter in San Antonio, Texas, from April 9–12.
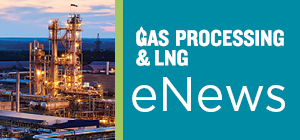
- ADNOC Gas awards $2.1 B in contracts to enhance LNG supply infrastructure
- U.S. Department of the Treasury releases final rules for clean hydrogen production tax credit
- Topsoe, Aramco sign JDA to advance low-carbon hydrogen solutions using eREACT™
- Nicor Gas celebrates its first renewable natural gas interconnection
- Phillips 66 outlines nearly $3-B capital program for 2025
Comments