Texas LNG picks Honeywell’s gas technology, automation for new project
Natural gas technology and process automation from Honeywell have been selected by Texas LNG, a Houston-based energy company, to remove contaminants from gas in preparation for liquefaction and export to global customers, officials announced on Thursday.
The two-phase project, located on the north shore of the Port of Brownsville's deep-water ship channel, will produce 4 million tons of liquefied natural gas (LNG) beginning in 2020.
“Honeywell is poised to support the growing global demand for LNG,” said John Gugel, vice president and general manager of Honeywell UOP’s gas processing and hydrogen business. “Honeywell’s integrated solution of advanced gas processing technology, combined with state-of-the-art automation and control systems, offers a streamlined approach to project execution that helps minimize project time, cost and risk. This approach will be critical in helping the project meet operational and business readiness goals at startup.”
Texas LNG will use Honeywell’s UOP Amine Guard FS process to reduce acid gas to very low levels and its proprietary adsorbents to remove water, mercury and sulfur from the natural gas, which is necessary for LNG transport. The Amine Guard FS process reduces carbon dioxide, hydrogen sulfide and other sulfur components from natural gas to very low levels, and the process can be customized depending on application and feed gas quality.
“As an independent liquefaction operator in a very competitive environment, bringing on board a company like Honeywell with such broad and integrated capabilities – proven in LNG – adds significant credibility and value to our venture," said Langtry Meyer, chief operating officer for Texas LNG. "We are confident this relationship will deliver over the long term for Texas LNG.”
More than 40% of treated LNG in the world is processed using Amine Guard FS technology. The UOP adsorbents can selectively adsorb contaminants by size and polarity, making them efficient agents for drying and purifying liquids and gases. The company’s GB series and HgSIV series adsorbents can be used in a number of combinations to remove mercury and minimize costs.
Honeywell Process Solutions (HPS), a leader in advanced automation and controls, will serve as the integrated main automation contractor (I-MAC). In this role, HPS is responsible for designing, delivering and installing the automation, instrumentation, controls, safety and security, operations management, and advanced planning and scheduling applications.
Honeywell is also assisting Texas LNG through the US Federal Energy Regulatory Commission’s (FERC) front-end engineering and design (FEED) process.
“With today’s large capital projects, leading technology companies must deliver value that goes beyond just providing technology on time and within budget. Honeywell is going even further and transforming the way major projects are designed and delivered,” said Pieter Krynauw, vice president for HPS’s projects and automation solutions business. “For this project, Honeywell’s integrated approach included consulting on FERC FEED, providing integrated technologies, solutions and services that will help the plant start up and reach optimum production faster, and implementing operations and supply chain optimization to exceed production plans. All of this will drive a step-change return on shareholder investment for our clients such as Texas LNG.”
Honeywell says it will help Texas LNG reduce risks and minimize potential schedule delays by using its integrated solutions including LEAP, Honeywell’s lean project execution services, Experion PKS with Distributed Systems Architecture (DSA), Experion Security Integrator, Fault Tolerant Ethernet (FTE), Universal process and safety I/O, virtualization, advanced control, Safety Manager, Fire and gas systems, OneWireless Network, Digital Video Manager (DVM), UniSim operator training simulator, DynAMo advanced alarm management software, and PHD data historian.
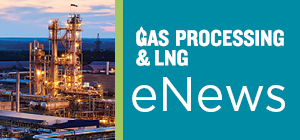
- ADNOC Gas awards $2.1 B in contracts to enhance LNG supply infrastructure
- U.S. Department of the Treasury releases final rules for clean hydrogen production tax credit
- Nicor Gas celebrates its first renewable natural gas interconnection
- EnviTec Biogas looks to expand biogas production into the U.S.
- Phillips 66 outlines nearly $3-B capital program for 2025
Comments