Gastech ’15: Printed circuit heat exchangers to unlock future of FLNG
By JOHN GAFFNEY
Heatric
SINGAPORE -- Printed circuit heat exchangers (PCHEs) are playing an important role in shrinking and lightening the topside bulk of the new global fleet of FLNG facilities.
In FPSO applications, PCHEs are already well-established as they help simultaneously tackle the three great offshore challenges: space, weight and safety. For existing platforms, PCHEs can be used to debottleneck and boost throughput. For new-build projects, like FLNG, compact heat exchanger technology offers the opportunity to design-in higher levels of process efficiency, safety and durability, unlocking many additional financial and operational benefits.
The limits of space. Ground-breaking FLNG vessels, such as Shell’s Prelude, are almost twice the size of the biggest FPSOs under construction. But not all FLNG vessels will be built on this scale, and even behemoths need to optimise their space, particularly given the precarious economics of “stranded” reserves. In other words, equipment footprint really matters in FLNG.
Meanwhile, topside bulk plays a big part in determining the operational effectiveness of even vast vessels like Prelude. Reduced topside weight lowers the centre of gravity, improving stability in heavy weather. The physical size of a PCHE unit (whether measured in terms of footprint, volume or weight) is often as much as 85% less than traditional technologies like shell and tube. This is due to an exceptionally high heat transfer-to-volume ratio, resulting in a smaller footprint for a given throughput. The ability to combine multiple processes within a single unit brings further space and energy savings.
The direct cost and space benefits of compactness are considerable. In projects like FLNG, as in FPSO and other offshore platforms, the very low size/weight envelope for a given duty allows PCHEs to unlock a “multiplier effect,” saving weight, complexity and substantial construction costs throughout the platform build process.
The core delivers savings and capabilities. An infinite variety of flow geometries can be designed into the flow channels of a PCHE, allowing every unit to be custom-designed to precisely match the heat transfer and pressure drop requirements of each application. Adjustments to path, diameter and wall-thickness can all be made to optimise for fluid types, in-process mixing, multiple liquid and gas combinations, temperature extremes, and pressure and wide differentials in the two. The finished plates are then diffusion bonded into a single block using a high temperature, solid state joining process that promotes grain growth across metal boundaries. The resulting joins exhibit the same strength and ductility as the parent-metal and are significantly stronger than a brazed or welded joint. Diffusion bonding also allows PCHEs to be made from a range of materials capable of delivering the corrosion resistance needed during a long, harsh life offshore.
Operations and safety. The high structural integrity and unique operating characteristics of this joint-less, self-supporting matrix of flow channels at the heart of every PCHE are of particular value to remote, floating processing applications. The “solid” heat transfer core results in a unit that can accommodate high effective duties (i.e., up to 98%) and with a very wide performance window—temperatures from cryogenic to 900⁰C (1650⁰F) and pressures as high as 650 bar (8,700 psi).
PCHEs can easily be designed to combine multiple integrated processes into a single unit, generating even greater savings. The use of two-phase inlets and careful channel design enable homogenous mixing of multiple flows without any risk of poor distribution. Because the PCHE design has discrete and separable fluid channels, multi-sectioned cores and/or headers can be designed to enable the unit to be maintained without shutdown in situations where frozen glycol, wax or hydrates may cause blockages.
The seamless core construction also minimises vibration fracture risks and renders PCHEs immune to the kind of catastrophic failure mode associated with shell and tube units. In the unlikely event of a leak, the etched design also ensures that escapes are 100 times smaller than an equivalent shell and tube leak. The entire PCHE is constructed from stainless steel or higher alloys (with no aluminium or other low-melting point materials used anywhere in the construction), so fire risks are also reduced.
Unlocking the future. The future shape and disposition of a fully-fledged global FLNG fleet remains to be seen, but while questions of scale will certainly be a key negotiable in the evolution of each new FLNG project, matters concerning safety and space optimisation will not. Whatever liquefaction choices an FLNG operator makes, PCHEs combine levels of compactness and robustness to deliver powerful solutions at the initial build stage, as well as exceptional debottlenecking and scale-up potential, all within an unmatched security and safety envelope of structural simplicity and strength.
Gastech 2015 continues through Friday in Singapore. As the official conference newspaper provider, stick with Gas Processing for continued live coverage from the event.
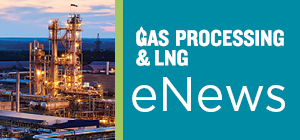
- ADNOC Gas awards $2.1 B in contracts to enhance LNG supply infrastructure
- U.S. Department of the Treasury releases final rules for clean hydrogen production tax credit
- Nicor Gas celebrates its first renewable natural gas interconnection
- EnviTec Biogas looks to expand biogas production into the U.S.
- Phillips 66 outlines nearly $3-B capital program for 2025
Comments