GTL ’15: GTC executives tout breakthrough in gas-to-chemicals technology
By Ben DuBose
Digital Editor
HOUSTON -- The new gas-to-aromatics technology acquired by GTC Technology in 2014 is changing the game for producing liquids from natural gas, according to director of global licensing at GTC.
Joseph Gentry, who spoke in Wednesday's early session at the GTL Technology Forum, explained that the latest GT-G2A technology is a novel means to convert natural gas to liquids using a methane coupling method of synthesis. The technology is also available for propylene (GT-G2P), butadiene (GT-G2BD) and EB/styrene (GT-G2EBS).
"This is a breakthrough technology using natural gas as the raw material for petrochemical production," Gentry said.
Historically, methane is activated and converted to higher hydrocarbons by the use of a co-reactant such as oxygen, halogens or sulfur. When oxygen is used as the co-reactant, as it is in many gas-to-liquids (GTL) and methanol-to-olefins (MTO) processes, the methane is activated to methanol or olefins, but the process is hampered by carbon production.
With the new technology, however, bromine is used as the agent to activate methane. Gentry says bromine is the ideal agent for the process, since it gives the highest carbon efficiency when building larger molecules. It also offers the opportunity to create a more diverse product slate, including aromatics.
The four-step process to convert the gas begins with bromination to methyl bromide, then a synthesis conversion to fuel and HBr, an HBr conversion to BR2, and then product separation -- largely into aromatics and diesel.
"The products from the synthesis reactor are mainly aromatics, butane, pentane and unreacted feed, along with bromine," Gentry said. "The products have a wide boiling point difference and are easily separable with minimum energy via simple fractionation."
The carbon efficiency of the gas-to-aromatics process is generally between 88% and 92%, Gentry noted.
Investigative lab work on this technology began in 2003, with the first demonstration unit constructed and operated in 2008 and 2009. The first commercial design began in 2010, paving the way for GTC's acquisition of the process in 2014.
"We like it because it offers the highest carbon efficiency of any commercial process," Gentry said. "It's profitable for both small-scale and large-scale projects."
Gentry showed a hypothetical capital expenditures (CAPEX) scenario with an MTO process at $1.72/KTA, a GTL process at $1.15/KTA and the GT-G2A process at only $0.95/KTA. Per ton of valuable product (OPEX), MTO would be $490/ton, GTL at $614/ton and GT-G2A at a mere $335/ton, Gentry said.
Moreover, GT-G2A offers superior economics at all natural gas prices, he said, along with the adaptability to produce all olefins and aromatics petrochemicals at any needed scale.
Going forward, GTC is looking for industry partners on the process, Gentry said. Project options would include licensing, basic engineering or FEED work; product offtake agreements; a joint investment by GTC and partners; and further technology partnerships.
The GTL Technology Forum continues through Thursday at City Centre in Houston.
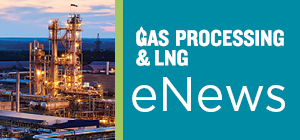
- Egypt agrees to buy up to 160 LNG cargoes through 2026
- Shell to add up to 12 MMt of additional LNG capacity by 2030
- ADNOC takes FID, awards $5 B in contracts for Phase 1 of its Rich Gas Development project
- U.S. ethane vessels stall amid curbs on exports to China
- TotalEnergies CEO expects to restart Mozambique LNG project this summer
Comments