Emerson Exchange ’14: Digital automation eased at midstream gas plant
By PRAMOD KULKARNI
Editor-in-Chief
ORLANDO, Florida -- Digital automation is hard enough under normal circumstances, but it can be a major reason for project delays and cost overruns, if the I/O requirements keep changing.
The digital automation system was installed at a 20 MMscfd cryogenic gas plant for Summit Midstream by Applied Control, an independent process automation provider active in the US Rocky Mountain region.
A presentation of how the project was managed through the extended series of change orders (COs) was made by Eric Siersma of Summit Midstream and Tyler Franzen of Applied Control at the Emerson Global Users Exchange taking place in Orlando.
The automation system consisted of an Emerson 650 DST DeltaV control system with electronic marshaling. The system I/O design flexibility comes from characterization modules (CHARMs) technology, which allows field wiring of any signal type to be terminated anywhere.
Instead of implementing the costly and complicated traditional approach of a pre-engineered physical wiring scheme, CHARMs technology provides a flexible approach that reduces the complexity of connecting automation systems with hundreds to thousands of devices in a typical process operation.
“At the DeBeque gas plant, the automation PO was received in April 2013, first CO in October 2013, and the DeltaV system configuration begun in November 2013,” said Franzen, explaining the rapid pace of construction and change orders. “The first compressor turnover and final loop checks were made in February 2014 and the system was released to the operator in March 2014.”
The automation system made use of two controllers—BPSCS (basic process controlled shutdown) and ESD (emergency shutdown). Four CHARMS enclosures were used, each with 192 I/O connections. Ultimately, 570 IO junctions were used.
“With conventional M series wiring, we would have spent $288,000,” said Siersma. “With the S series electronic marshalling, we’ve spent $70,000 less, saved three to four weeks of time, and also gained significant reconfiguration flexibility.”
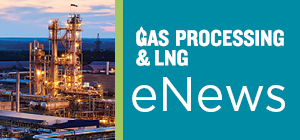
- Egypt agrees to buy up to 160 LNG cargoes through 2026
- TotalEnergies CEO expects to restart Mozambique LNG project this summer
- TotalEnergies and CMA CGM to launch LNG bunkering logistics JV to accelerate maritime decarbonization
- Renergen awards EPCC contract for Tetra4 LNG and helium project
- thyssenkrupp nucera acquires modular high-pressure electrolysis solution from Green Hydrogen Systems
Comments