2014 GTL Technology Forum brings executive insight, new developments
By ADRIENNE BLUME
Managing EditorHOUSTON -- Gulf Publishing Company's second annual Gas-to-Liquids (GTL) Technology Forum opened Wednesday and continues through Thursday. Speakers and attendees shared insight on gas processing technology developments, project economics and business challenges, with a focus on GTL processing technologies. A full news roundup from technical sessions and a photo gallery are included below:
NEWS STORIES
GTL ’14: US ethane wave boosts outlook for ammonia producers (Day 2)
GTL ’14: North America gas projects challenged by worker shortage (Day 1)
GTL ’14: Fluor suggests placing GTL units inside refineries (Day 1)
GTL ’14: CompactGTL chief details small-scale progress, impediments (Day 1)
Day 2 of the second annual GTL Technology Forum, which drew nearly 200 attendees from the US and a number of other countries, opened with an ExxonMobil-sponsored networking breakfast in the exhibition hall. Exhibitors Pentair, Siemens, AMACS, Walter Tosto and Ariel discussed their products and services with forum delegates over coffee, pastries and fruit.
EIA assessment of US GTL. After the breakfast, Vishakh Mantri of the US Energy Information Administration (EIA) delivered a keynote presentation on the economics of GTL conversion technologies.
Dr. Mantri reviewed the EIA's Annual Energy Outlook research methodology and how the government body makes its projections. He then discussed why natural gas is an ideal fossil fuel in terms of emissions, sulfur content and available infrastructure, and what other fuels are competing with GTL fuels. Competing fuels include petroleum fuels refined from crude oil, CNG, LNG, and plant-based biofuels.
Dr. Mantri also talked about the EIA's categorization of projects. Greenfield projects require full development of land and infrastructure prior to the start of construction, and all process units, including utilities, are part of the project. CO2 emissions and water disposal are included in pricing.
On the other hand, infrastructure is usually already in place at brownfield developments. Minimum land preparation is required, and utilities may be shared. Dr. Mantri also emphasized that high capital cost is a major roadblock to profitable production of liquid fuels at GTL plants in the US.
Ammonia from offgas. Dr. Mantri's keynote was followed by a presentation by V.K. Arora, director of process and operations for Kinetics Process Improvements Inc., on the economics of ammonia production from offgases. As Mr. Arora explained, ammonia production from offgases is a well-known process, but it is not widely practiced.
The shale gas boom has produced excess ethane, spurring producers to crack more ethane to make ethylene. In the US, eight new ethane crackers are planned for construction, with startup dates between 2016 and 2018. More hydrogen has been produced with increased ethane cracking, enabling greater output of low-cost ammonia.
However, this scenario has resulted in the loss of propylene and heavier products. The industry has responded with on-demand propylene production, with plans to build more propane dehydrogenation (PDH) units. Six PDH units are in the works, with a total capacity of more than 3.5 MMtpy.
Process options for ammonia production include pressure swing adsorption, nitrogen wash, secondary reforming, secondary reforming with O2 enrichment, and secondary reforming with gas-heated reforming. Each process option has pros and cons, Mr. Arora explained.
The ammonia production potential from each process scheme varies, with the highest production coming from secondary reforming of ethane, using either O2 enrichment or gas-heated reforming—two processes that are relatively new to the marketplace. The two new processes also yield environmental benefits, such as a 33% reduction in NOX emissions from the source plant.
Session 4: Emerging technology. The fourth session, which was chaired by Syamal Podder, president of Podder & Associates, was opened by Peter Tjim, CTO of Standard Alcohol Co. of America Inc. Dr. Tjim explained how mixed alcohols can be used as oxygenates and fuel extenders.
A solution to RFS and the gas glut. The US Renewable Fuel Standard, which requires the blending of increasing amounts of biofuels into domestic gasoline and diesel supplies through 2022, is under scrutiny, as it is reducing gasoline demand and hurting the US refining industry. Dr. Tjim suggested that the market, rather than political forces, be allowed to determine how fuel supply should be diversified.
Due to massive oversupply of natural gas in the US from unlocked shale gas reserves, domestic gas prices are expected to remain depressed well into the future, making gas uneconomical to produce. A solution to these issues is to produce drop-in, Environment Protection Agency-approved alternative oxygenates, additives and fuel extenders from natural gas, thereby reducing emissions and supporting the refining industry.
Mixed alcohols produced from natural gas are biodegradable in soil and water, not crop dependent like biofuels, require less energy to produce than crop-based ethanol, result in fewer vehicle tailpipe emissions, and are produced through a carbon-neutral process, Dr. Tjim explained. Standard Alcohol, which has been testing its catalysts at its partners' labs for several years, is in the process of planning its first commercial mixed alcohol production plant.
The MTG alternative. Following Dr. Tjim's talk, Terry Helton, catalyst product manager in technology sales and licensing for ExxonMobil Research and Engineering (EMRE), shared details on methanol-to-gasoline (MTG) technology as an updated alternative for liquid fuel production.
The MTG process, which produces 87-octane, pipeline-grade gasoline with extremely low benzene content and no sulfur, is a demonstrated technology that is offered by a number of commercial technology providers. The process can be easily integrated into an existing methanol plant with the addition of an intermediate tank, Dr. Helton explained.
EMRE has made significant advancements in the implementation of MTG technology since its inception decades ago, and it recently acquired a number of new licenses for the process.
Session 5: Catalysts. The catalysts session was chaired by the author, following a packed networking lunch. Avinash Karre, process engineer at Jacobs Engineering, talked about the effect of adding zeolite to iron-based catalysts for Fischer-Tropsch (FT) synthesis. Cobalt catalysts are costly compared to iron catalysts, Mr. Karre said.
In his research, he compared an activated carbon base catalyst to a ZSM-5 catalyst, in both separate-bed and mixed-bed formations. ZSM-5 catalysts favor cracking reactions. Productivities were found to be lower in a mixed-bed arrangement vs. a single-bed arrangement. Some metals migration may be present in the ZSM-5 catalyst, which could account for the lower productivity, Mr. Karre said.
FT reactor downsizing with new catalyst. Tom Holcombe, president and CEO of Green Impact Fuels, then summarized the new CatFT process. Challenges in the Fischer-Tropsch (FT) process include heat management, tight control of catalyst temperature, scalability to small applications, productivity of cobalt catalysts and reduction of capital costs. The US Air Force, which funded the construction of the first CatFT pilot plant, is working with Green Impact Fuels to design small, modular, mobile systems.
The benefits of the CatFT design, Dr. Holcombe explained, include a thin catalyst coating, which requires less catalyst at a lower cost; heat conductivity by fins, which results in faster heat removal and tight temperature control; lower gas velocities, which give lower pressure drop through the reactor and enable the use of a smaller, shorter reactor and smaller compressors; as well as lower CAPEX and OPEX, particularly with regard to off-the-shelf evaporators. The process is also scalable to smaller applications, with proven profitability at plants as small as 100 bpd.
Advances in fixed-bed reactors. Lastly, Vice President of Gas Conversion for Johnson Matthey (JM) Davy Technologies Ltd., Tim Gamlin, spoke on the topics of fixed-bed reaction systems for FT technology and JM Davy's collaboration with BP on its demonstration plant in Nikiski, Alaska.
JM Davy's compact reformer is characterized by several advantages, including modular and factory-built equipment that can be shipped as a bundle and which generates low NOX emissions. Mr. Gamlin also emphasized the lack of catalyst movement in the fixed-bed arrangement.
The company has succeeded in increasing catalyst productivity, improving C5+ selectivity and extending catalyst life for its reactor system. Among the areas for improvement in fixed-bed FT is the relatively large size and weight of the reactors, which can be problematic for land-locked sites with little access to water, Mr. Gamlin explained.
Session 6: Modular construction. The forum's final session included an overview of global GTL construction projects by Lee Nichols, director of Gulf Publishing Company's data division, as well as a panel discussion on modular construction, moderated by Mr. Nichols. Panelists included Raj Suri, president of EmberClear; Jeff McDaniel, commercial director of Velocys; and Iain Baxter, COO of CompactGTL.
GTL project roundup. Mr. Nichols explained that the US has far surpassed the rest of the world in new gas processing project announcements, with 39% of the global share in 2014. Asia-Pacific, which saw the second-highest percentage of new project announcements in 2014, is expected to surpass Europe as the world's second-largest gas market within a few years.
At present, there are four commercial-sized GTL projects in operation around the world, with two more in development. However, the major trend seen in the US for GTL operations is small-scale projects. Thirteen GTL projects are in the works along the Gulf Coast, in the Northeast, and in the Midwest and West. Additionally, small-scale GTL developments are planned outside of the US in Kazakhstan, Russia, Canada, Bolivia and Brazil.
The path to GTL development. During the panel discussion, Mr. Suri addressed questions of practicality for GTL developments, including financing in the face of questions about technology viability, gas price volatility and production economics. Mr. Baxter agreed that challenges remain. "I don't, in fact, think GTL is taking off yet in North America," he said.
Mr. Baxter also referred to Mr. Gamlin's presentation on new developments in conventional FT, noting the need for a "mid-scale technology to fill the gap between small-scale GTL and world-scale GTL" to help GTL gain traction in the US marketplace.
Meanwhile, Mr. McDaniel touted small-scale GTL as the primary trend in GTL today. He sees growing opportunities for additional GTL projects after the main challenges to development—many of which were raised by forum speakers—are addressed and solved.
GTL Technology Forum 2015. In closing, Stephany Romanow, editor of Hydrocarbon Processing, thanked attendees, speakers and the advisory board for making the second GTL Technology Forum a success. The third annual GTL Technology Forum will be held in summer 2015 in Houston
DAY 1 SESSION ROUNDUP
Session 1: Syngas. The technology sessions of the Day 1 agenda kicked off with an introduction by V. K. Arora, director of process and operations at Kinetics Process Improvements, who served as the session chair for the syngas portion of the program.
Autothermal reforming. In one part of the syngas session, Soren Martin Olsen, sales manager for Haldor Topsøe, talked about autothermal reforming (ATR) as a preferred technology for the conversion of natural gas to syngas in industrial GTL applications. The price gap between gas and oil is rising, so the incentive for converting gas into chemicals and transportation fuels—such as methanol, gasoline and diesel—is increasing, Mr. Olsen explained.
ATR technology, which has been in industrial operation for more than 10 years, includes optimized catalysts and loading schemes. The world's largest ATR units are in operation at the Oryx GTL plant in Qatar. Improvements to the ATR technology have been continuously implemented. Today, both the technology and operation are very stable and robust, with good carbon efficiency and an excellent onstream factor, Mr. Soren said.
Turboexpander syngas generation. Dr. Steven Fusselman, program manager of energy services for Aerojet Rocketdyne, and Dr. Arunabha Basu of the Gas Technology Institute (GTI), co-presented on partial oxidation gas turbine-based syngas generation technology for GTL applications. This technology describes the replacement of the waste boiler with a rotating machine (i.e., the turboexpander) at a high temperature.
GTI's patented Turbo-POX GTL process, which operates under significantly higher pressure than conventional systems, features improved overall efficiency and lower liquid production costs. In the turboexpander, regenerator-cooled stator blades provide higher system efficiency than film-cooled blades. The existing design is sized for 1 Mbpd of liquids production capacity. "The POX unit was designed with an eye toward simplification. As we know, these units don't scale down that gracefully," Mr. Fusselman acknowledged.
Dr. Basu discussed the techno-economics of the Turbo-POX technology. Key advantages for Turbo-POX vs. catalytic ATR are the close-coupled POX reactor and expander, which are ideal for shop fabrication and modular small-scale GTL plants. Also, no catalytic pre-reformer and no catalyst are needed for the POX reactor.
The technical sessions were punctuated by a well-attended buffet lunch, where delegates engaged in technology and business discussions over hearty beef and fish dishes, as well as light salads and pastas, and cheesecake and coffee for dessert.
Integrating small-scale GTL. Paul Koppel, vice president of process technology at Fluor, spoke about the feasibility of mega-GTL vs. small-scale GTL, and how small-scale GTL can be integrated into existing refining and petrochemicals operations. Various considerations for a generic large-scale GTL plant configuration include carbon emissions and capture, water supply and treating, byproducts (i.e., alcohols, naphtha and LPG) and alternative higher-value products (i.e., waxes and lube oils).
Mr. Koppel compared financial returns for large-scale GTL projects in operation to small-scale project estimates, listing revenues for Pearl GTL, Sasol in Louisiana and a GTL project in Uzbekistan. Small-scale projects give high per-barrel returns, although their small capacities limit the amount of money that can be made from the fuels produced. Large-scale plants have good per-barrel returns and large capacities that guarantee high revenues. Small-scale projects take a fraction of the time to construct as do large-scale plants.
To keep capital expenditure (CAPEX) costs low for small-scale GTL, a simplified process scheme is preferred. Location questions must also be answered. Should the plant be remote and operate as a standalone unit, or can it use infrastructure and utilities from an existing facility?
As Iain Baxter did in his keynote address, Mr. Koppel examined factors holding up the widespread implementation of small-scale GTL. Gas producers and banks are often unwilling to take a risk on new entrepreneurial project developers without large capital sources or large balance sheets to support financing, especially for new, non-commercialized Fischer-Tropsch (FT) GTL technologies.
However, when small-scale GTL facilities are placed inside an existing facility, there is the possibility of excess syngas capacity for GTL operations, the potential availability of CO2, the availability of an existing hydrocracker for upgrading, and the availability of existing utilities, offsites and services. These advantages make the implementation of small-scale GTL projects within existing refineries and petrochemical plants a good solution, Mr. Koppel said.
Session 2: Non-FT GTL. After the lunch break, the day continued with a session on the future of non-FT GTL. Session chair Stephany Romanow, editor of Hydrocarbon Processing, introduced Dr. Michael Schultz, vice president of engineering at LanzaTech Inc., who spoke about a biological route for converting waste CO2 into fuels and chemicals. Gas fermentation can be integrated with methane conversion in LanzaTech's proprietary process, as has been shown in six successful technology demonstrations at industrial sites in New Zealand, Asia and the US.
The company is working on its first commercial plant with BaoSteel in China. The initial target for commercial production is approximately 70 M gal of gasoline equivalent per day of ethanol, at a gas cost of around $3/MMBtu.
"We really look at this approach as a way of industrial growth," Mr. Schultz said. "We know that growth needs to continue, and the question is, how can we do so sustainably, in a way that doesn't compete for land and which allows emerging economies to grow."
Drop-in GTL fuels at small scale. Next, Dr. George Boyajian, vice president of business development for Primus Green Energy, spoke about the conversion of natural gas into drop-in liquid fuels at small scale. Mr. Boyajian opened his talk by noting that his meetings at the inaugural GTL Technology Forum in 2013 led to important developments for which Primus will be making announcements in the near future. "As an unsolicited testimony … You can get deals done at this meeting," Mr. Boyajian asserted.
Primus is eyeing the startup of its first commercial plant in 2016, which will use syngas feedstock to produce drop-in synthesis gasoline. Primus is also developing gas-based diesel fuel in the lab, which it will scale up to the demonstration-plant scale in the near future.
The company has gathered important results from its first demonstration plant in New Jersey. "We've reduced the piece count in our plant by 50%. So, that means fewer things to go wrong and lower capital costs," Mr. Boyajian attested. An amine unit, which was originally thought to be essential to operation, has been removed from the plant design.
With greater than 99% availability, the demonstration plant produced more than 6 M gal of high-octane gasoline, with no off-spec product. Additionally, it recorded no process downtime, with the exception of a compressor repair. Primus expects catalyst regeneration to be required only once a year.
The products from the plant contain zero sulfur and zero benzene, and they fit ASTM specifications for gasoline. The units are built on skids and then shipped to the site. Studies have shown that the Primus process is the most cost-effective process, in terms of CAPEX and OPEX, for capacities of under 6 Mbpd, Mr. Boyajian said. The plants can consist of units with capacities of 2 Mbpd in several trains, as 2 Mbpd is the largest-capacity reactor that can fit under a highway overpass.
FT vs. non-FT. Closing out the second session, Ajey Chandra, managing director for Muse, Stancil & Co. in Houston, talked about FT GTL vs. non-FT GTL. Mr. Chandra acknowledged that the growing demand for high-quality fuels, coupled with an increase in gas supply, is enabling GTL technology to change the energy landscape.
FT processes dominate existing projects, but there are some new, non-FT technologies and projects coming to the industry. There will be a race for commercialization, especially in light of the gas price volatility seen in the US over the last 10 years. It is critical to examine the ratio between the liquid products and the gas value in determining GTL economics, Mr. Chandra said. Capital cost considerations for a standalone GTL plant are highly dependent on technology selection, project size, project location and other factors.
The director also noted that many of the drop-in GTL diesel fuels being produced today are better used as blendstocks, based on their specifications. In fact, blending with other fuels may be a more lucrative route for drop-in fuel producers, he said. In the US diesel market, there is demand growth and opportunity for only the highest-quality products, especially with regard to exports.
"Right now is one of the best times we have to do these GTL projects because of the fact that we've got shale gas," Mr. Chandra said, in closing. However, he also advised investors to study how long shale gas drilling will continue, and whether gas prices will remain stable and predictable.
Session 3: Small-scale developments. Syamal Podder, president of Poddar & Associates, chaired the last session of the day on new developments in smaller-scale GTL. Jeff McDaniel, the commercial director of Velocys, opened the session with a talk on smaller-scale GTL production from microchannel FT reactors. He shared the latest results from the company's pilot plant operations and discussed joint venture developments.
The results from Velocys' integrated GTL pilot plant in Ohio show good catalyst productivity and stable temperature results over 1,000 hours of operation, with one shutdown at around 500 hours for a steam system repair.
Additionally, Velocys is working with Waste Management, NRG Energy and Ventech Engineering to develop GTL fuels from landfill gas in the US, UK, Canada and China. A final investment decision was made in July to go ahead with the first demonstration plant, which will be built in Oklahoma. Velocys is also collaborating with Ventech on an integrated modular GTL diesel production unit.
Velocys is also developing a 2.8-Mbpd brownfield plant with Ashtabula GTL, and a 2.5-Mbpd biomass-to-liquids plant with Red Rock Biofuels to produce jet fuel. Lastly, the company is targeting a US Department of Defense grant for another biomass-to-liquids project, for which a decision will be made in August.
GTL project wrap-up. The two final speakers of the day were Raj Suri, president of EmberClear, and Walter Breidenstein, CEO of Gas Technologies LLC. Mr. Suri gave an update on a GTL project in Natchez, Mississippi. EmberClear, a project development company, specializes in the fast turnaround of energy projects of 18 months or less.
Mr. Breidenstein closed out Day 1 with a short presentation on Gas Technologies LLC's single-step gas-to-methanol technology, which is designed to help solve the gas flaring problem in North Dakota. The "well-to-wheel" solution is low-cost, portable and addresses 100% of the flare, Mr. Breidenstein said.
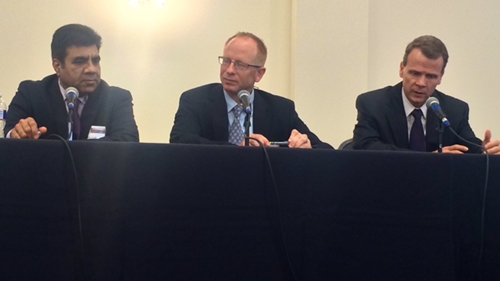
president of EmberClear; Iain Baxter, executive director of CompactGTL;
and Jeff McDaniel, commercial director of Velocys.
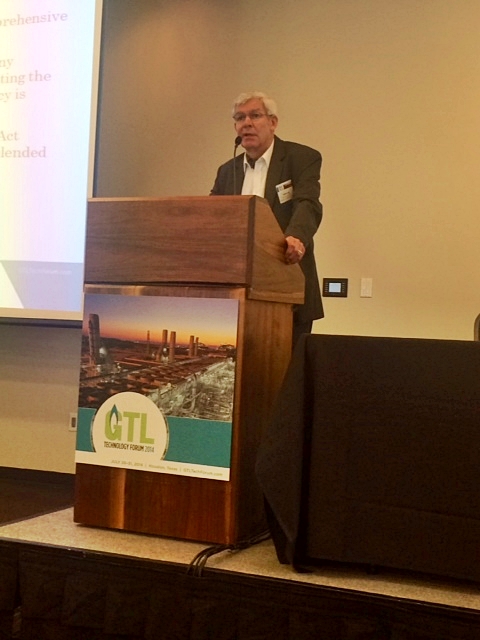
of mixed alcohols as an oxygenate and fuel extender during Thursday's Session Four.
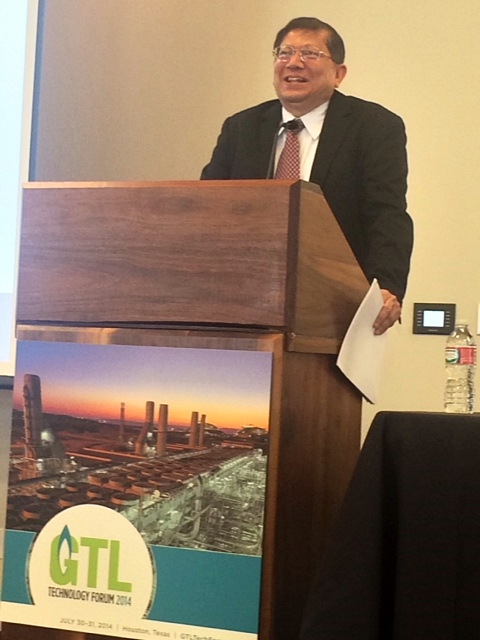
The US Energy Information Administration's (EIA) Vishakh Mantri gave Thursday's
keynote address regarding the economic outlook of GTL conversion technologies.
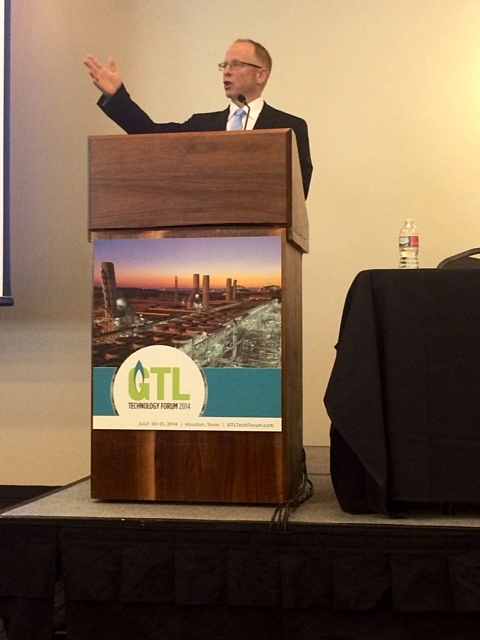
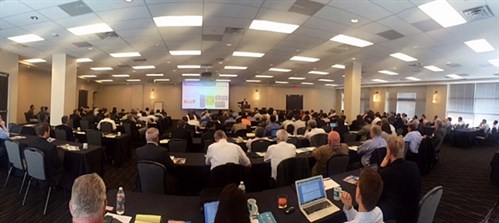
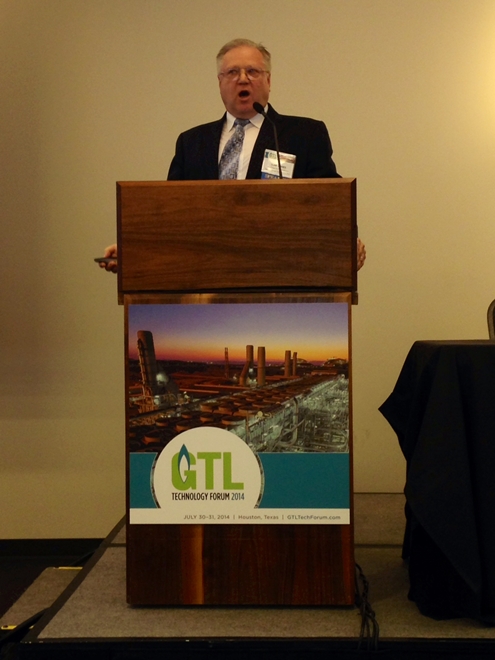
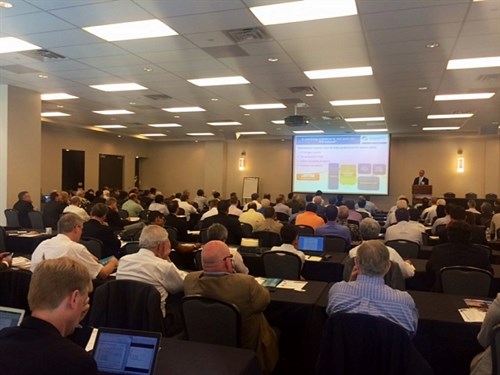
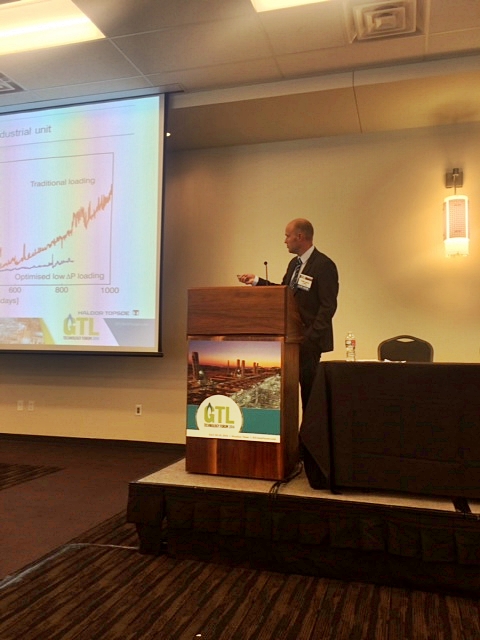
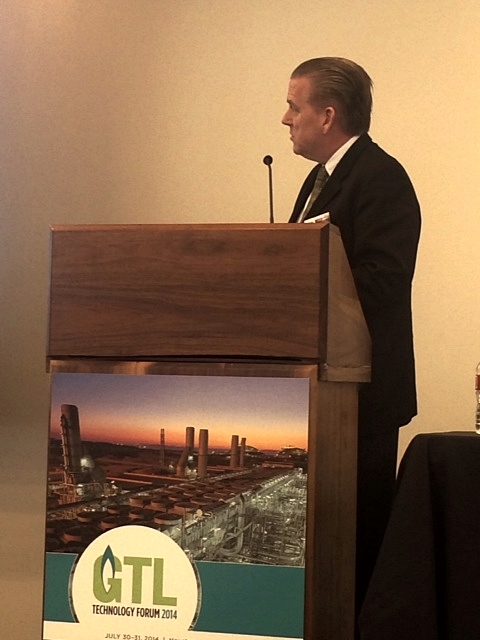
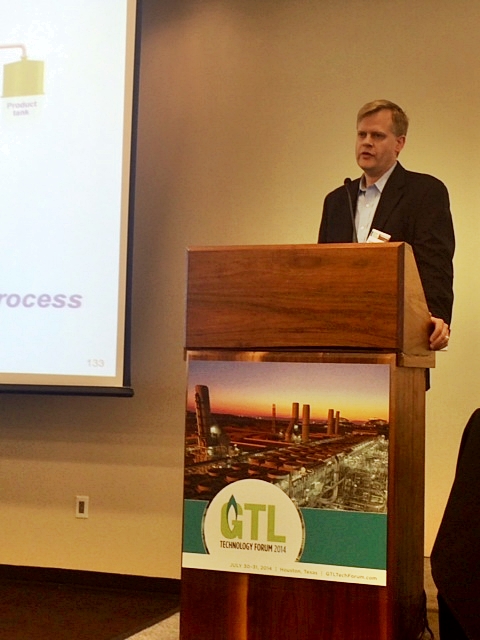
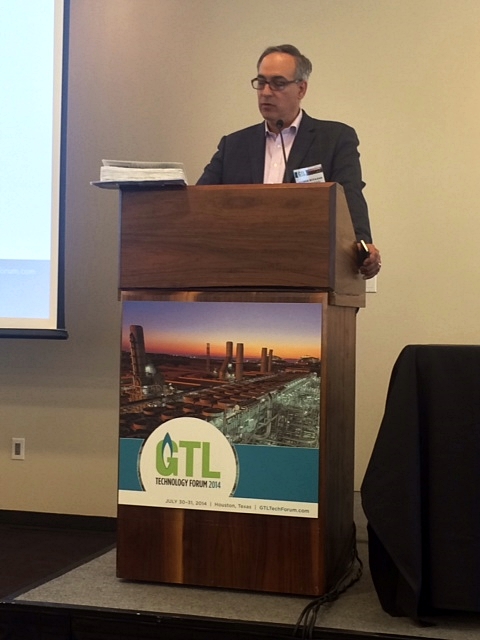
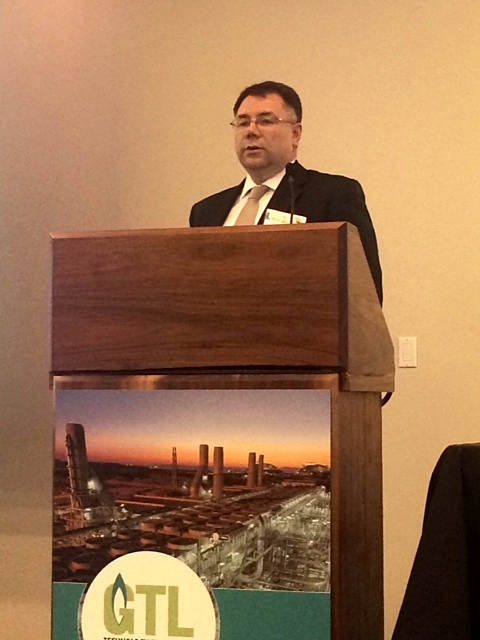
Comments